Projekt zu geschlossenem Rohstoffkreislauf startet
Ein Konsortium von zwölf Partnern aus Wirtschaft und Wissenschaft startet unter Führung der Volkswagen AG das vom Bundesministerium für Wirtschaft und Klimaschutz geförderte Projekt zu geschlossenem Rohstoffkreislauf „HVBatCycle“. Ziel ist die dauerhafte Rückgewinnung wertvoller Materialien zur Erhöhung von Nachhaltigkeit und Versorgungssicherheit. Die gewonnenen Rohstoffe können in einem geschlossenen Kreislauf wiederverwendet werden. Die Partner wollen gemeinsam nachweisen, dass die wertvollsten Bestandteile von Antriebsbatterien durch Recycling mehrfach nacheinander zurückgewonnen und wiedereingesetzt werden können.
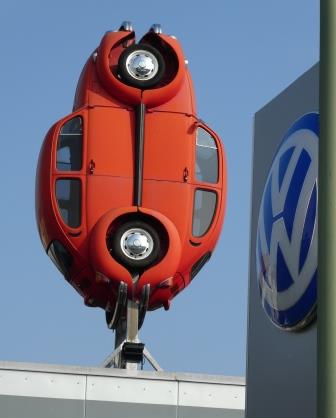
Die wertvollsten Bestandteile von Antriebsbatterien sollen durch Recycling mehrfach nacheinander zurückgewonnen und wiedereingesetzt werden können – Foto © Gerhard Hofmann, Agentur Zukunft für Solarify
Das Forschungskonsortium „HVBatCycle“ hat das Ziel, Kathodenmetalle, Elektrolyt und Graphit dauerhaft im geschlossenen Materialkreislauf (Closed Loop) zu führen. Unter Führung des Volkswagen Konzerns arbeiten TANIOBIS GmbH, J. Schmalz GmbH, Viscom AG zusammen mit Forschern von RWTH Aachen University, TU Braunschweig sowie Fraunhofer-Institut für Schicht- und Oberflächentechnik (IST) drei Jahre lang an der Erforschung und Entwicklung der dafür erforderlichen Prozesse. Das Projekt wird vom Bundeswirtschaftsministerium für Wirtschaft und Klimaschutz gefördert.
Michael Kellner, Parlamentarischer Staatssekretär: „Die europäische Batterie-Produktion kann nur erfolgreich sein, wenn sie in möglichst allen Bereichen auf Nachhaltigkeit setzt. Nachhaltige Batterien sind entscheidend für eine Energie- und Verkehrswende, die sich an hohen Umwelt- und Sozialstandards orientiert.“
Sebastian Wolf, Chief Operating Officer Battery Volkswagen AG, erklärte: „Das Recycling von Batterien und Produktionsausschüssen trägt entscheidend dazu bei, die Rohstoffversorgung unserer geplanten Fabriken sicherzustellen. Durch das Projekt HVBatCycle wird eine ganzheitliche Betrachtung der Recyclingprozesse und dadurch die Umsetzung des Closed Loop der Batteriematerialien vorbereitet.“
Geschlossener Rohstoffkreislauf und mehrfaches Recycling
Um weniger Materialien aus primären Quellen wie Minen oder Salaren nutzen zu müssen, sollen wesentliche Rohstoffe nicht nur einmal, sondern gleich mehrfach zurückgewonnen werden. Dazu werden Batteriezellen aus recyceltem Material nochmals recycelt, um damit außerdem nachzuweisen, dass auch mehrfache Recyclingdurchläufe keinen Einfluss auf die Materialqualität haben. Das Schließen des Kreislaufs erfordert komplexe interdisziplinäre Prozesse. Für eine effiziente, ökologisch und ökonomisch sinnvolle Verwertung müssen alle Verfahren aufeinander abgestimmt sein, um unter höchsten Sicherheitsanforderungen sortenreine und qualitativ hochwertige Sekundär-Materialien zu erzeugen. Dabei geht es insbesondere um Skalierbarkeit und Wirtschaftlichkeit.
Unabhängigkeit durch Dezentralisierung, Vorteile durch Einsatz von Sekundärmaterialien
Im Konsortialprojekt steht die mechanisch-hydrometallurgische Recyclingroute im Fokus, die sich durch einen geringen Energiebedarf und die Möglichkeit zu einer vergleichsweise einfachen dezentralen Verteilung bestimmter Recyclingprozesse in Europa auszeichnet. Das begünstigt eine lokale Kreislaufwirtschaft und sichert strategisch wichtige Rohstoffe, was die Abhängigkeit Europas von anderen Regionen der Welt deutlich reduziert. Das Projekt „HVBatCycle“ soll effiziente Verfahren und innovative Lösungen aufzeigen, die den Aufbau einer End-to-End Wertschöpfungskette mit hoher Wirtschaftlichkeit bei gleichzeitig möglichst hoher Recycling- und Energieeffizienz und minimalen Umweltbelastungen gewährleisten.
Automatisierung der Demontageprozesse und Rückgewinnung des Elektrodenmaterials
Konkrete innovative Entwicklungsansätze liegen in einer bedarfsgerechten, d.h. wirtschaftlich optimierten Entladung und einer weitgehend automatisierten Demontage von rückläufigen Batteriesystemen bis auf Zell- oder Elektrodenebene. Dazu zählt auch eine nahezu verlustfreie Trennung von Aktivmaterial und Trägerfolien sowie die Rückgewinnung von Graphit und leichtflüchtiger Elektrolytbestandteile.
Bei der folgenden hydrometallurgischen Aufbereitung der „Schwarzen Masse“ aus Graphit und Batteriemetallen durch Wasser und chemische Lösemittel steht eine frühe und selektive Extraktion des Lithiums in löslicher Form sowie die Laugung, Fällung und Raffination enthaltener Metalle als Mischhydroxid-Konzentrat im Vordergrund. Dabei soll in Zusammenhang mit der erneuten Materialsynthese von kathodischem Aktivmaterial untersucht werden, ob die Auftrennung von Metallverbindungen wirklich erforderlich ist, um neues, vollumfänglich leistungsstarkes Kathodenmaterial herzustellen.
Die Forschungsarbeiten zur Aufbereitung des Elektrolyten und des Graphits sollen durch die Entwicklung von geeigneten Verfahren zeigen, dass auch wichtige Elektrolytbestandteile und das Graphit effizient aufbereitet und wieder in batterietauglicher Qualität in der Zellproduktion eingesetzt werden können. Sämtliche Verfahrensschritte werden ganzheitlich von einer ökologischen und wirtschaftlichen Lebenszyklusanalyse begleitet.
Über die Kooperationspartner:
Die Volkswagen AG ist im Rahmen ihrer Batteriestrategie und ihrer Nachhaltigkeitsstrategie sehr stark an der Verwirklichung eines geschlossenen Kreislaufs (Closed Loop) von Zellmaterialien interessiert und hat deshalb die Koordination und Steuerung des Projektes übernommen. Das Konzernressort Technik sorgt mit der Pilotanlage zum mechanischem Recycling am Komponenten-Standort Salzgitter für die Erzeugung und Bereitstellung von recyclingfähigem Material aus Fahrzeugbatterien. Darüber hinaus
wird die Zellfertigungs-Kompetenz des Centers of Excellence in Salzgitter genutzt, um aus vollständig recyceltem Material neue Zellen zu produzieren.
Die TANIOBIS GmbH ist Qualitätsanbieter für Niob- und Tantal-haltige Pulver für hydrometallurgische Herstellungsverfahren einschließlich Solventextraktion. Als Tochter der JX Nippon Mining & Metals sind bei ihr tiefgehende Kenntnisse im hydrometallurgischen Recycling von Lithium-Ionen-Batterien vorhanden, die im Projekt genutzt werden sollen. Darauf basierend wird die TANIOBIS GmbH die benötigte hydrometallurgische und pyrometallurgische Infrastruktur am Standort Chemiepark Oker errichten und betreiben, wo auch ein zertifiziertes Analyselabor zur Verfügung steht.
Die J. Schmalz GmbH ist der weltweit führende Anbieter für Vakuum-Technologie und einer der wenigen Komplettanbieter in diesem Bereich. Schmalz liefert im Geschäftsfeld Vakuum-Automation alle Vakuum-Komponenten, um Greifer für Industrieroboter aufzubauen. Darüber hinaus gewährleistet Sensorik von Schmalz Prozesseffizienz und -sicherheit. In gemeinsamen Projekten mit wissenschaftlichen Instituten konnten Handlingsysteme für Siliziumwafer, Kathoden- und Anodenfolien etabliert werden.
Die Viscom AG entwickelt Röntgenmesslösungen speziell für den Einsatz in der Batteriezellindustrie. Das Produktportfolio reicht von Laborsystemen bis hin zur kompletten Inline-Lösung für die 100%ige Qualitätskontrolle bei hohen Geschwindigkeiten. Viscom ist spezialisiert auf eine Vielzahl unterschiedlicher Zellformate, wie z. B. Pouch- oder prismatische Zellen, die verschiedene Größen für Consumer-Produkte über Energiespeicher bis hin zu E-Mobility-Zellen abdecken.
Die Battery LabFactory (BLB) als etabliertes transdisziplinäres Forschungszentrum der TU Braunschweig ist eine der federführenden Einrichtungen im Bereich der Batterieforschung in Deutschland. Die BLB ist eine F&E-Plattform für zirkuläre Produktion, Diagnostik und Modellierung/Simulation von Batterien heutiger und zukünftiger Generationen. In ihrem Pilottechnikum bündelt die BLB ingenieurwissenschaftliches Prozess-Know-how, materialwissenschaftliche Expertise, naturwissenschaftliches Batteriezellsystemwissen und fundierte analytische Kompetenzen.
Das Institut für Werkzeugmaschinen und Fertigungstechnik (IWF) fokussiert sich auf technologische und automatisierungstechnische Fragestellungen entlang aktueller und zukünftiger Fertigungsprozessketten von Batteriezellen.
Das elenia Institut für Hochspannungstechnik und Energiesysteme verfügt über weitreichende Erfahrungen im Bereich der Formierung, der zyklischen Alterung sowie der elektrischen und elektrochemischen Charakterisierung von Batteriezellen.
Am Institut für Partikeltechnik (iPAT) werden mechanische und partikeltechnische Prozesse zur Herstellung von Batteriematerialien und –elektroden sowie mechanische und thermische Prozesse zum Batterierecycling untersucht.
Das Institut für Chemische und Thermische Verfahrenstechnik (ICTV) besitzt breite Expertise zur Trennung fluider Stoffgemische.
Das Institut für Energie- und Systemverfahrenstechnik (InES) verfügt über langjährige Erfahrung in der Modellierung und Simulation von Batterien sowie der elektrochemischen Analyse und Operando-Analytik.
Das Fraunhofer-Institut für Schicht- und Oberflächentechnik (IST) forscht und entwickelt intensiv in den Bereichen Materialsynthese und -funktionalisierung, Oberflächenbehandlung und -modifikation, Schichtherstellung und -anwendung, Schichtcharakterisierung und Oberflächenanalyse sowie im Bereich der Produktionstechnik. Die Batterieforschung als zentrales Thema im Fraunhofer-Projektzentrum für Energiespeicher und Systeme fokussiert auf die Material- und Energiespeicherentwicklung einschließlich zugehöriger Verfahrens- und Fertigungstechniken sowie der ganzheitlichen und nachhaltigen Gestaltung des Lebenswegs.
Die RWTH Aachen University, Institut für Metallurgische Prozesstechnik und Metallrecycling (IME), hat langjährige Erfahrung in der anwendungsorientierten Erforschung von Batterierecyclingprozessen. Dabei liegt der Forschungsschwerpunkt auf der Rückgewinnung der in Batterien enthaltenen Wertmetalle mit Hilfe thermischer und hydrometallurgischer Prozesse. Das Institut hält eine umfassende Infrastruktur zur Erprobung verschiedener Recyclingkonzepte vor, die auch einen innovativen Pyrolyseofen der Firma Otto Junker GmbH zur Verarbeitung größerer Mengen bzw. ganzer Batteriemodule beinhaltet. Über das hauseigene zertifizierte Labor stehen dem IME viele wichtige Analyseverfahren, die bei der Untersuchung möglicher Batterierecyclingprozesse benötigt werden, zur Verfügung.
->Quelle: Volkswagenag.com/de/news/2022/06/volkswagen-led-research-team-to-recycle-batteries-multiple-times