Aber: Wie Stickstoff mit weniger Druck und Hitze fixieren?
Ammoniak, wichtige Chemikalie in Landwirtschaft und Industrie (inzwischen auch als klimaneutraler Zukunftstreibstoff), ist zwar giftig und riecht stechend, wird aber seit 1913 in großem Maßstab (jährlich weltweit 180 Millionen Tonnen) nach dem Haber-Bosch-Verfahren hergestellt, industriell aus Distickstoff und Dihydrogen mit Hilfe heterogener Katalysatoren unter harten Reaktionsbedingungen (bis 500° C und 350 bar). Die Umweltauswirkungen dieses Prozesses (Dihydrogen aus fossilen Brennstoffen, mit dem Nebenprodukt Kohlendioxid), bei dem Methan als Brenn- und Ausgangsstoff für Wasserstoff verwendet wird, begründeten die Notwendigkeit einer nachhaltigeren Ammoniakproduktion: Daher ist die Entwicklung eines synthetischen Ansatzes zur Herstellung von Ammoniak, bei dem keine fossilen Brennstoffe verwendet werden, unter dem Gesichtspunkt der Nachhaltigkeit besonders wünschenswert. Viele Strategien, die erneuerbaren Wasserstoff verwenden, sind jedoch nicht mit den bestehenden Verfahren zur Ammoniakabtrennung kompatibel.
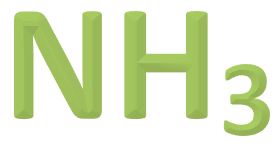
NH3 – Ammoniak-Formel
Aufgrund ihrer großen Oberfläche und ihrer strukturellen und chemischen Vielseitigkeit sind metallorganische Gerüste (MOFs) vielversprechend für die Ammoniakabtrennung, aber die meisten MOFs binden Ammoniak irreversibel oder bauen sich ab, wenn sie diesem korrosiven Gas ausgesetzt sind. Ein abstimmbares dreidimensionales Gerüst bildet ein dichtes, eindimensionales Koordinationspolymer, das Ammoniak reversibel bindet, indem es sich kooperativ in seine Metall-Carboxylat-Bindungen einfügt. Dieser ungewöhnliche Adsorptionsmechanismus bietet ein beträchtliches intrinsisches Wärmemanagement, und bei hohen Drücken und Temperaturen führt die kooperative Ammoniakaufnahme zu großen Arbeitskapazitäten.
Eine Gruppe der Max-Planck-Gesellschaft für Kohleforschung in Mühlheim an der Ruhr hat bereits vor eineinhalb Jahren ein Verfahren entwickelt und open access in nature publiziert, das sogar bei Raumtemperatur und Normaldruck Ammoniak erzeugt. Als Reaktor nutzen sie eine Kugelmühle, in der die mechanische Reibung der Kugeln die chemische Reaktion antreibt. Doch ist der Weg einer vielversprechenden Entwicklung bis hin zur großtechnischen Anwendung oft lang: Erst in den Neunzigerjahren wurde ein abgewandeltes Verfahren in Betrieb genommen, das statt Fritz Habers ursprünglichen Eisen-Katalysators einen aus Ruthenium nutzt.
Da die Synthese von Ammoniak aus atmosphärischem Distickstoff, die Stickstofffixierung, ist derzeit (noch) auf Dihydrogen aus fossilen Brennstoffen als Rohstoff angewiesen ist, ist die Entwicklung einer Stickstofffixierungsreaktion, die auf der Energie erneuerbarer Energien wie sichtbarem Licht beruht, ein wichtiges Forschungsziel unter dem Gesichtspunkt der nachhaltigen Chemie. Japanische Chemiker haben nun einen Iridium- und Molybdän-katalysierten Prozess zur Synthese von Ammoniak aus Distickstoff unter Umgebungsbedingungen und Bestrahlung mit sichtbarem Licht enwickelt. In diesem Reaktionssystem wirken Iridiumkomplexe und Molybdäntrijodidkomplexe mit N-heterozyklischen Carben-basierten Pincer-Liganden als kooperative Katalysatoren zur Aktivierung von 9,10-Dihydroacridin bzw. Distickstoff. Die Reaktion von Distickstoff mit 9,10-Dihydroacridin ist thermodynamisch nicht begünstigt und findet nur unter Bestrahlung mit sichtbarem Licht statt. Daher handelt es sich bei dem Reaktionssystem um eines, bei dem die Ammoniakbildung aus Distickstoff katalytisch durch die Energie des sichtbaren Lichts angetrieben wird. (Nature Communications: nature.com/articles/s41467-022-34984-1)
Ammoniak könnte die intelligentere Lösung für den Transport von Wasserstoff über große Entfernungen sein, nicht nnur, weil er nicht explosionsgefährdet iat. Da er bei 4 bar schon bei Raumtemperatur flüssig ist, entfällt der zur Verflüssigung von Wasserstoff nötige gigantische Energieaufwand: Für minus 254°C, müssen 30 bis 40% der Energiemenge des verflüssigten Wasserstoffs aufgewandt werden. Aber für „grünen“ Dünger ist es zu teuer.
->Quellen: